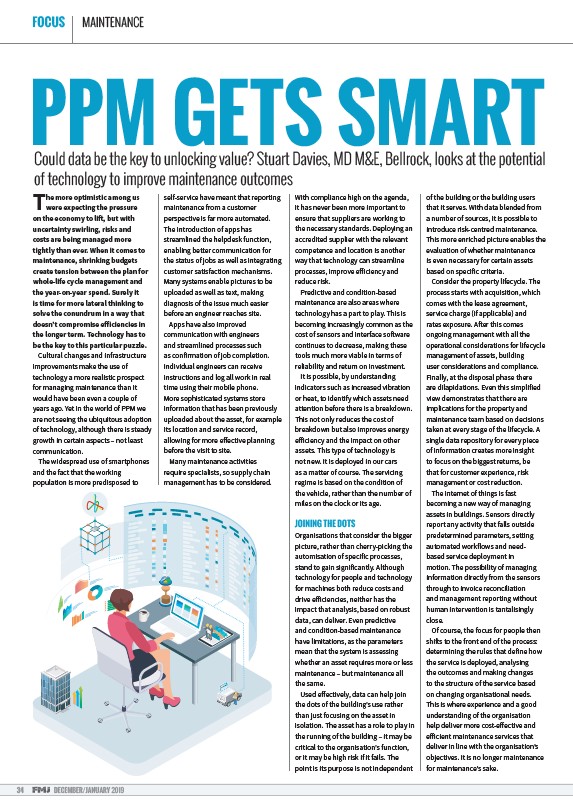
FOCUS MAINTENANCE
PPM GETS SMART
Could data be the key to unlocking value? Stuart Davies, MD M&E, Bellrock, looks at the potential
of technology to improve maintenance outcomes
The more optimistic among us
were expecting the pressure
on the economy to li , but with
uncertainty swirling, risks and
costs are being managed more
tightly than ever. When it comes to
maintenance, shrinking budgets
create tension between the plan for
whole-life cycle management and
the year-on-year spend. Surely it
is time for more lateral thinking to
solve the conundrum in a way that
doesn’t compromise e iciencies in
the longer term. Technology has to
be the key to this particular puzzle.
Cultural changes and infrastructure
improvements make the use of
technology a more realistic prospect
for managing maintenance than it
would have been even a couple of
years ago. Yet in the world of PPM we
are not seeing the ubiquitous adoption
of technology, although there is steady
growth in certain aspects – not least
communication.
The widespread use of smartphones
and the fact that the working
population is more predisposed to
34 DECEMBER/JANUARY 2019
self-service have meant that reporting
maintenance from a customer
perspective is far more automated.
The introduction of apps has
streamlined the helpdesk function,
enabling better communication for
the status of jobs as well as integrating
customer satisfaction mechanisms.
Many systems enable pictures to be
uploaded as well as text, making
diagnosis of the issue much easier
before an engineer reaches site.
Apps have also improved
communication with engineers
and streamlined processes such
as confirmation of job completion.
Individual engineers can receive
instructions and log all work in real
time using their mobile phone.
More sophisticated systems store
information that has been previously
uploaded about the asset, for example
its location and service record,
allowing for more e ective planning
before the visit to site.
Many maintenance activities
require specialists, so supply chain
management has to be considered.
With compliance high on the agenda,
it has never been more important to
ensure that suppliers are working to
the necessary standards. Deploying an
accredited supplier with the relevant
competence and location is another
way that technology can streamline
processes, improve e iciency and
reduce risk.
Predictive and condition-based
maintenance are also areas where
technology has a part to play. This is
becoming increasingly common as the
cost of sensors and interface so ware
continues to decrease, making these
tools much more viable in terms of
reliability and return on investment.
It is possible, by understanding
indicators such as increased vibration
or heat, to identify which assets need
attention before there is a breakdown.
This not only reduces the cost of
breakdown but also improves energy
e iciency and the impact on other
assets. This type of technology is
not new. It is deployed in our cars
as a matter of course. The servicing
regime is based on the condition of
the vehicle, rather than the number of
miles on the clock or its age.
JOINING THE DOTS
Organisations that consider the bigger
picture, rather than cherry-picking the
automisation of specific processes,
stand to gain significantly. Although
technology for people and technology
for machines both reduce costs and
drive e iciencies, neither has the
impact that analysis, based on robust
data, can deliver. Even predictive
and condition-based maintenance
have limitations, as the parameters
mean that the system is assessing
whether an asset requires more or less
maintenance – but maintenance all
the same.
Used e ectively, data can help join
the dots of the building’s use rather
than just focusing on the asset in
isolation. The asset has a role to play in
the running of the building – it may be
critical to the organisation’s function,
or it may be high risk if it fails. The
point is its purpose is not independent
of the building or the building users
that it serves. With data blended from
a number of sources, it is possible to
introduce risk-centred maintenance.
This more enriched picture enables the
evaluation of whether maintenance
is even necessary for certain assets
based on specific criteria.
Consider the property lifecycle. The
process starts with acquisition, which
comes with the lease agreement,
service charge (if applicable) and
rates exposure. A er this comes
ongoing management with all the
operational considerations for lifecycle
management of assets, building
user considerations and compliance.
Finally, at the disposal phase there
are dilapidations. Even this simplified
view demonstrates that there are
implications for the property and
maintenance team based on decisions
taken at every stage of the lifecycle. A
single data repository for every piece
of information creates more insight
to focus on the biggest returns, be
that for customer experience, risk
management or cost reduction.
The internet of things is fast
becoming a new way of managing
assets in buildings. Sensors directly
report any activity that falls outside
predetermined parameters, setting
automated workflows and needbased
service deployment in
motion. The possibility of managing
information directly from the sensors
through to invoice reconciliation
and management reporting without
human intervention is tantalisingly
close.
Of course, the focus for people then
shi s to the front end of the process:
determining the rules that define how
the service is deployed, analysing
the outcomes and making changes
to the structure of the service based
on changing organisational needs.
This is where experience and a good
understanding of the organisation
help deliver more cost-e ective and
e icient maintenance services that
deliver in line with the organisation’s
objectives. It is no longer maintenance
for maintenance’s sake.